Protein processing – Service and maintenance
Minimize the risk of unplanned downtime and loss of raw material with Alfa Laval as your service partner. We offer a complete range of services spanning the entire lifetime of your plant, and our service engineers are always ready to support you when you need quick and professional help. Using a systems approach to service, our service engineers help maximize the performance of your entire process, not just its individual parts.
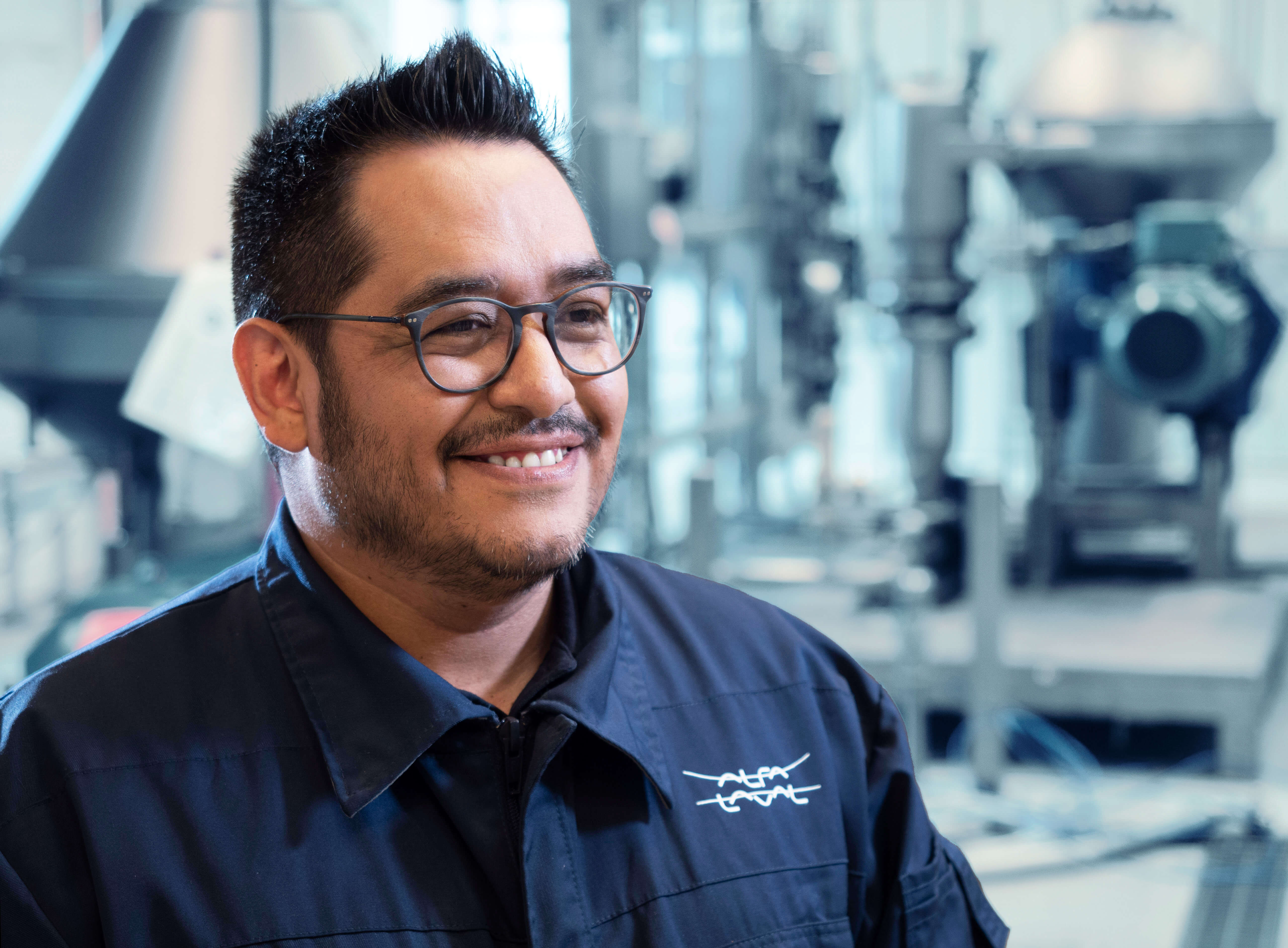
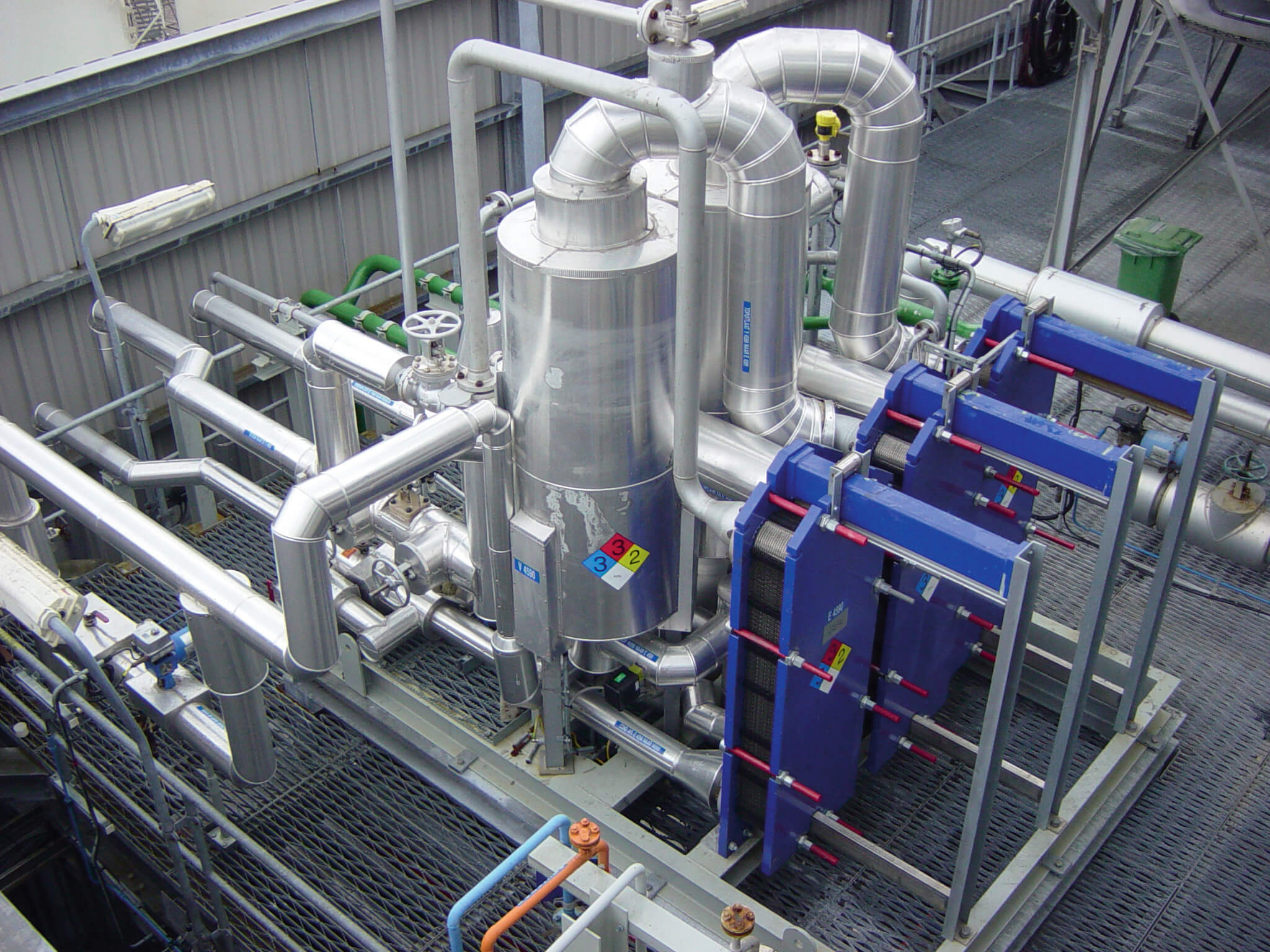
Troubleshooting on a system level
The root cause of a problem in one part of your process can often be found in another part of the plant. Therefore, our service engineers always have a holistic approach when identifying and fixing problems.
For instance, if the output from your evaporation system has the wrong concentration, there are several possible causes:
- A problem in the evaporation system itself.
- The viscosity of the evaporation system’s input stream is wrong due to problems in the cooking stage.
- The decanter and/or separator capacity is too low.
Another example is if you experience high maintenance costs for your separator. This may be due to insufficient capacity in the decanter, resulting in a high solids load on the separator.
Contact Alfa Laval if you are experiencing problems in your plant, and we will help you find the underlying causes.
Local support with a global scope
Presence is key to good support. Our unmatched service network combines a strong local focus with a global reach, covering close to 100 countries.
Our field service engineers are just a phone call away, ready to assist you on site and in your local language. They are supported by our global team of process specialists, our network of service centres, and spare parts hubs, ensuring you always have immediate access to professional support and genuine spare parts.
For customers operating protein processing systems on ships, we can offer service onboard or in the nearest harbour if required.
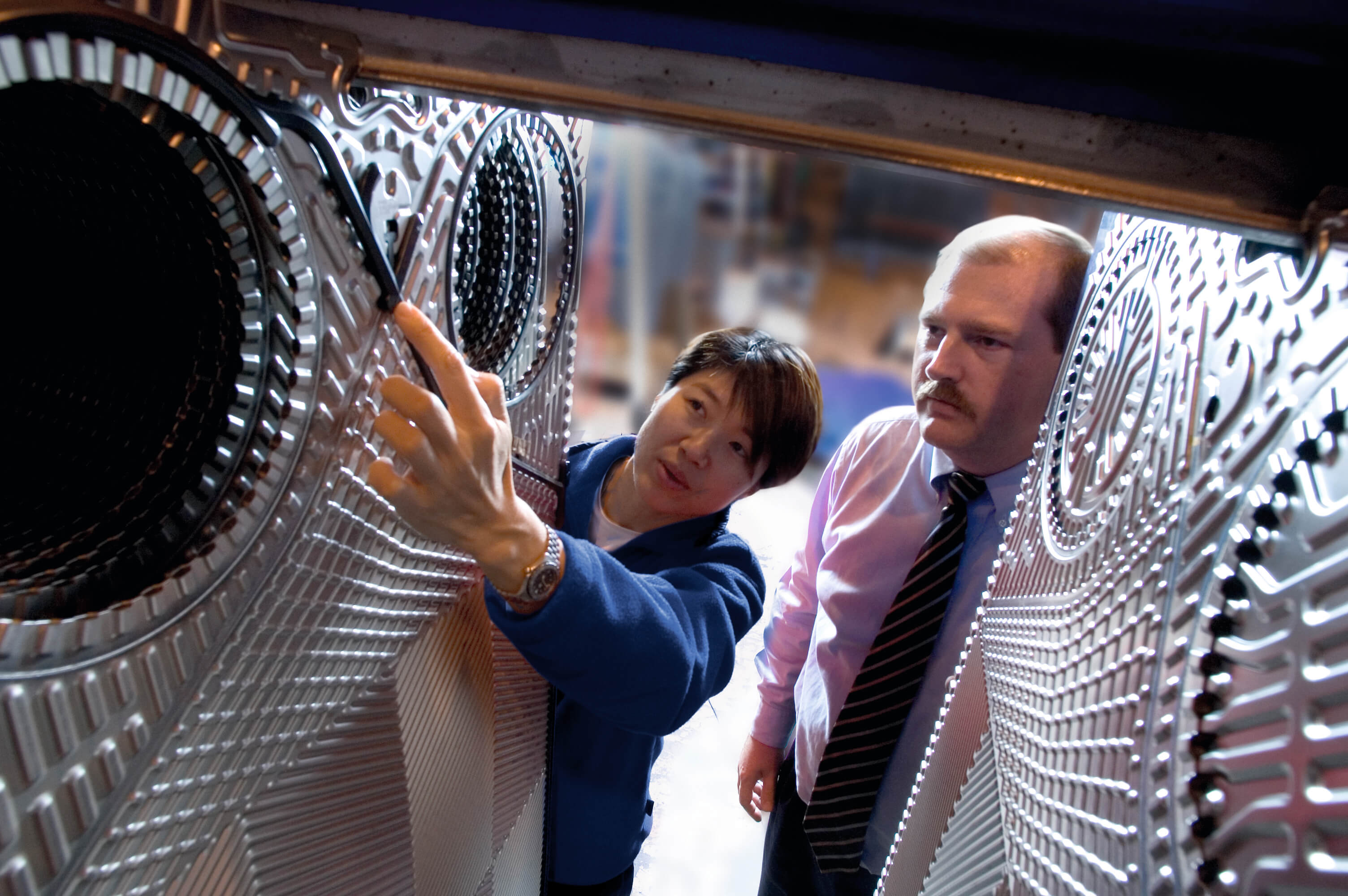
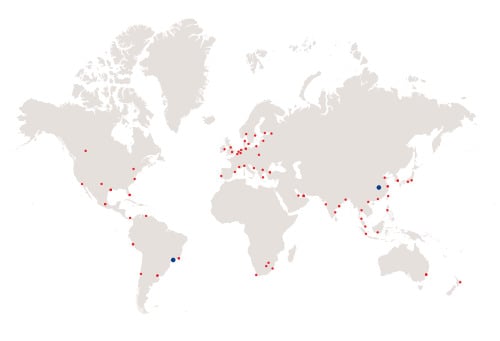
Do you need our help
If you need our help and wish to contact us, please visit our service page to find the contact details for your local service office. You can also click the link below to fill out our service contact form, and we will contact you shortly.
Fill out our service contact form
Fully tailored service solutions
For maximum uptime and predictable cost, we recommend signing up for an Alfa Laval Service Agreement. These fully customized service solutions can include any of our services, and we manage all aspects of planning, execution, and spare parts procurement. The benefits include:
- No risk of OPEX and CAPEX overrun
- Maximum uptime
- Higher product quality
- Minimal risk of health and safety incidents
- Lower cost for service
- Higher yield thanks to maximal output and minimal product loss
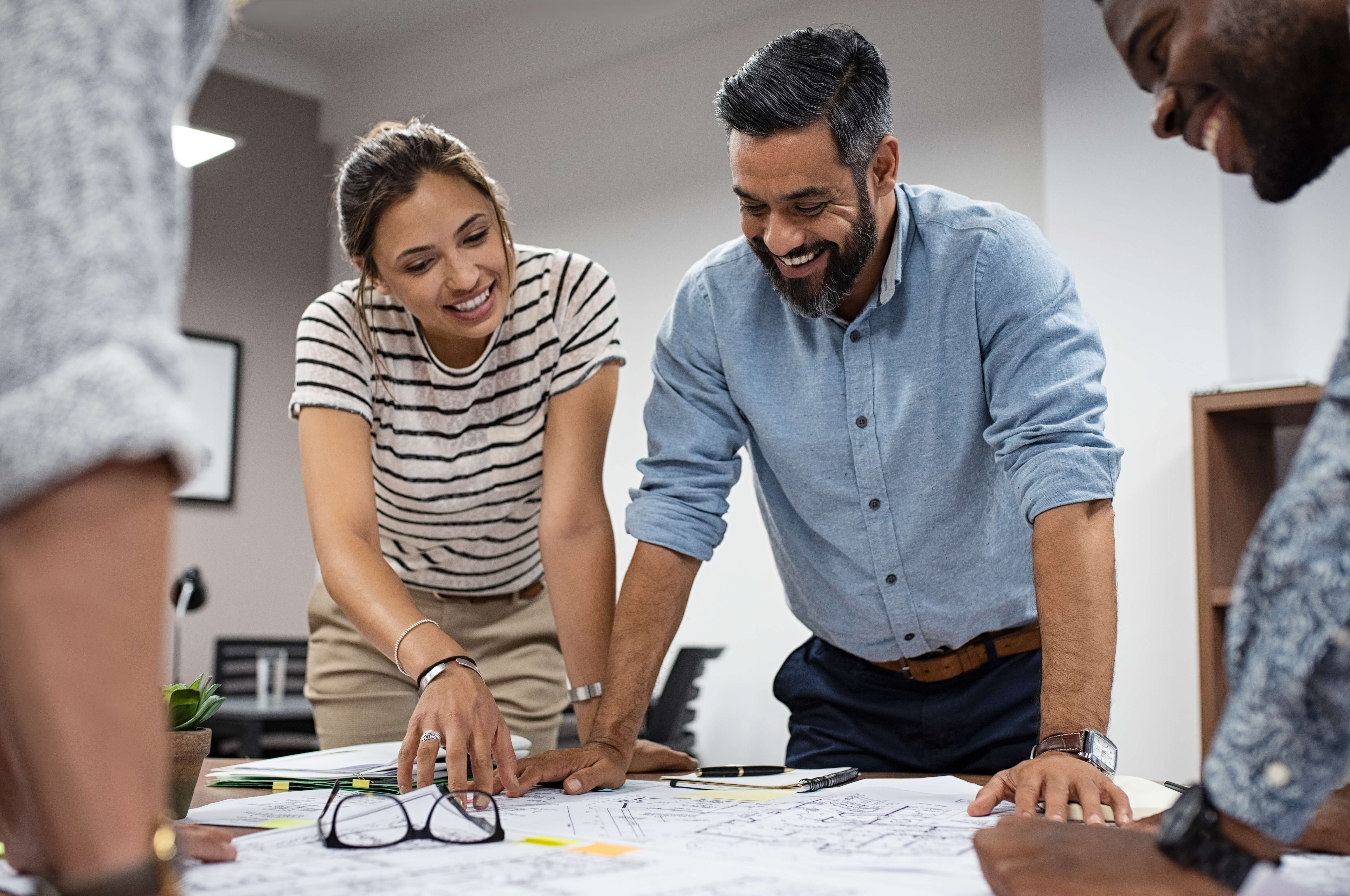
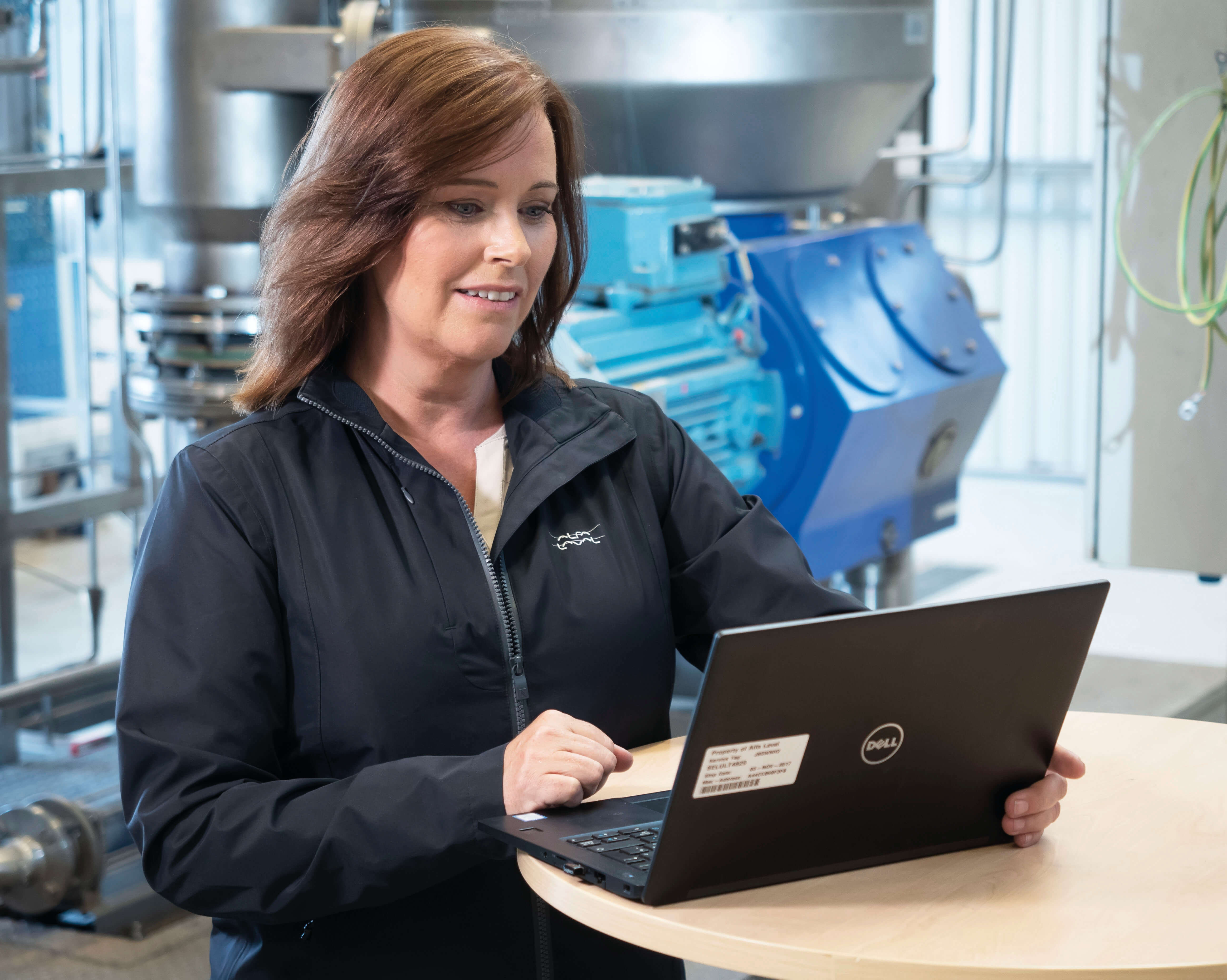
Performance Audits
A Performance Audit provides you with valuable insights into the condition and performance of your protein processing equipment on both a system and component level.
The information from a Performance Audit allows you to:
- Optimize service intervals to minimize cost
- Maximize operational reliability
- Ensure high performance, product quality, and process yield
In addition, you will receive recommendations on improvements to your system and its operation.
Ensuring sustainable operation
Regular maintenance is essential for keeping your system operating efficiently. Wear, fouling, and unnecessary friction all result in higher energy consumption, having a negative effect on both your bottom line and the environment. Servicing your equipment at regular intervals allows you to identify such issues at an early stage and take proactive measures to resolve them.
Older systems can benefit from upgrades that reduce energy consumption and add new functionalities such as recovery of by-products and water.
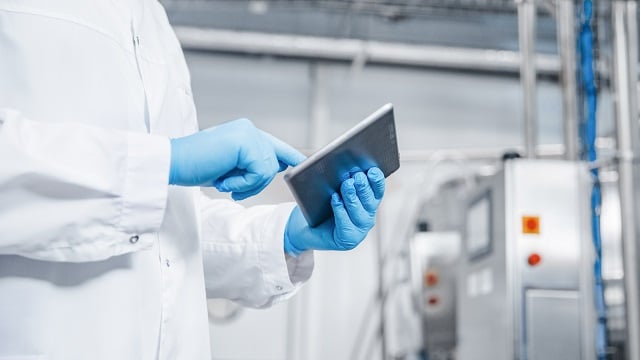
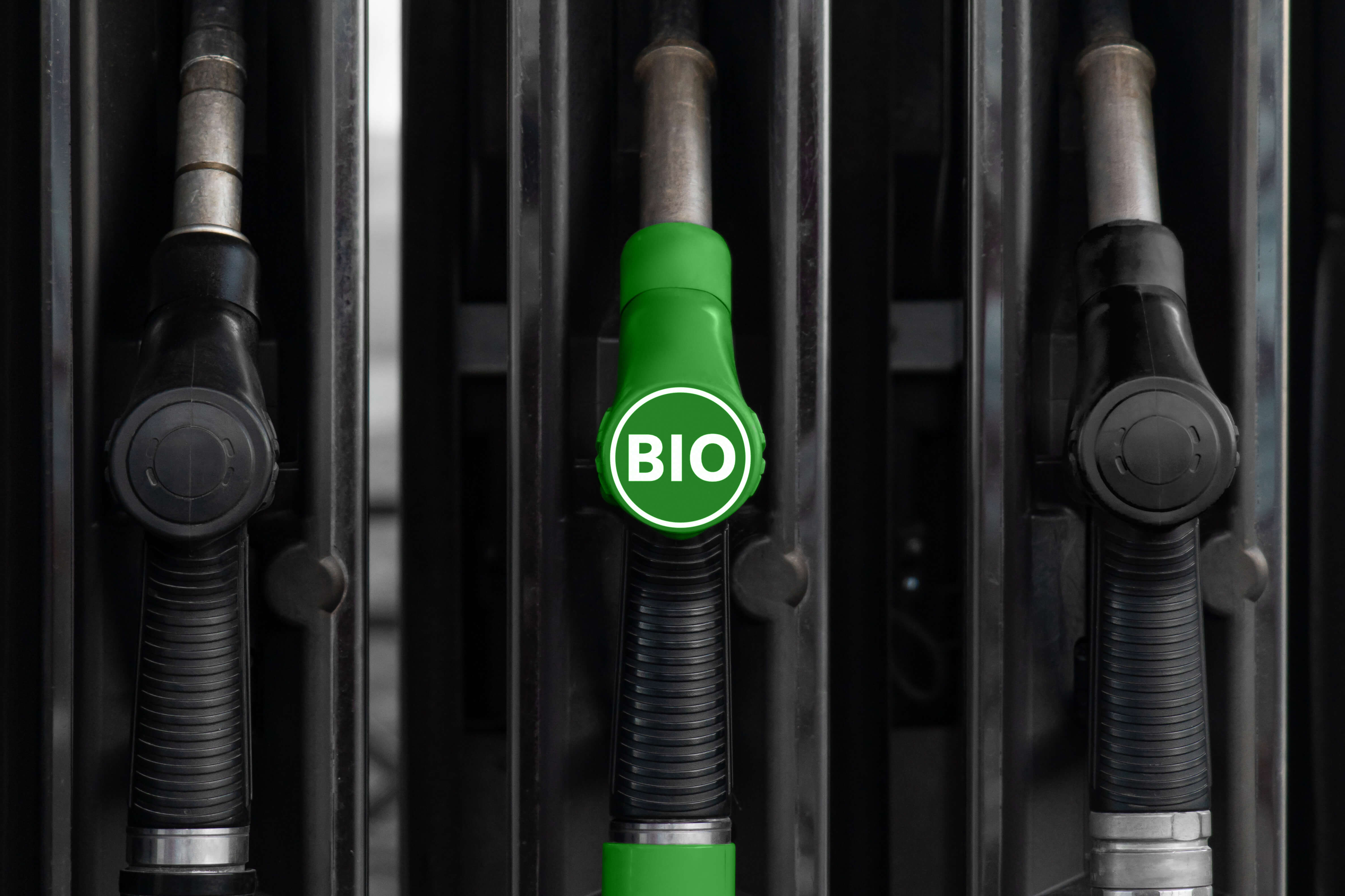
Cut energy cost and profit on the biofuel/HVO boom with upgrades
The service life of a protein processing plant spans several decades, during which markets and conditions are likely to change. We help you continuously upgrade your system to meet these changes and maximize the long-term return on your investment.
For instance, several of our existing customers are upgrading their systems to increase fat recovery to monetize on the biofuel/HVO trend. Others are upgrading to improve energy efficiency and limit the impact of rising energy prices. Upgrades can also bring advantages such as increased capacity, higher product quality, and new revenue streams from recovering by-products.
All the services you need – from maintenance to upgrades
The Alfa Laval 360° Service Portfolio includes everything you need to keep your equipment performing at top level over time:
- Installation and commissioning
- Preventive maintenance
- Repairs
- Reconditioning
- Troubleshooting
- Genuine spare parts
- Condition monitoring services
- Performance audits
- Predictive maintenance and condition monitoring
- Remote support
- Upgrades and redesigns
- Retrofits
- Training
- Preventive maintenance programmes
- Reactive maintenance services
- Maintenance and repair services