Cellular agriculture systems – Upstream processing
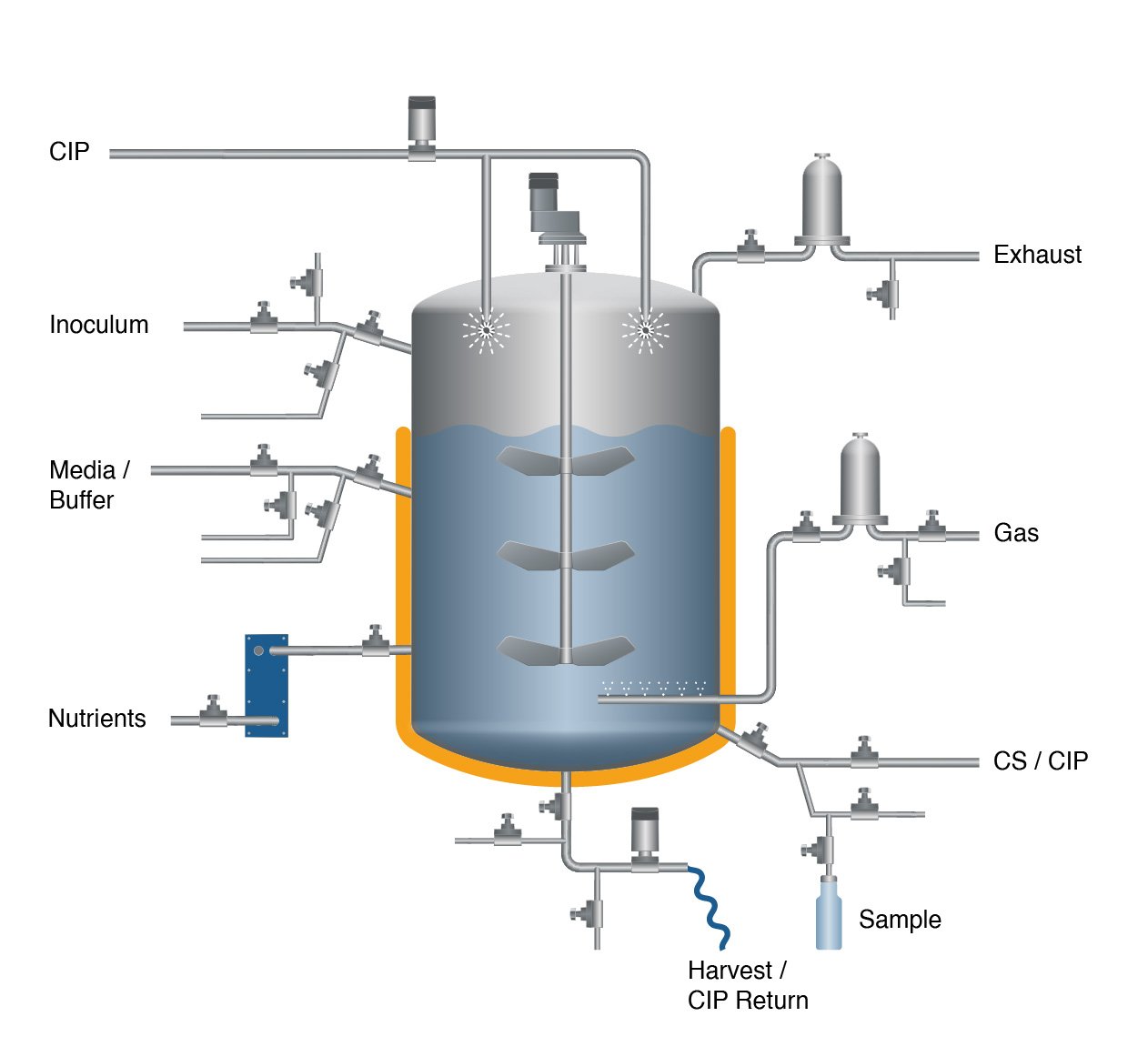
The bioreactor is the heart of any cellular agriculture process. This is where the initial raw materials are converted into valuable products. Bioreactors must have systems in place to control parameters such as temperature, pH, oxygen, and sterility to facilitate the growth of the microorganisms. Since each microorganism favours its own specific conditions, the design of the bioreactor must be tailored to the microorganisms used in the process to maximize yield and product quality.
Alfa Laval has a long experience in bioreactor design and can provide custom-made bioreactors for all types of fermentation processes and applications, regardless of the type of microorganism used.
We can provide seed fermenters and primary fermenters with the necessary:
- Agitation – The contents of the bioreactor must be thoroughly mixed at any given time to ensure an even distribution of nutrients and gas to every cell in the bioreactor. In addition, agitation is needed to ensure there are no pockets with too high/low temperatures or pH values. Creating the optimum agitation is a critical design task, but at the same time one must ensure that the shear stress on the cells is not excessive.
- Gas supply – Whether it is oxygen or another gas, it is crucial to design sparging systems that ensure optimal transfer of the gas from the bubbles into the culture medium, making it accessible to the microorganisms. It is also important to filter the incoming gases to ensure sterility.
- Inoculation – Every bioreaction (fermentation) starts with the inoculation. Inoculation is the process of introducing a preculture with cells from a seed fermenter or a shake flask. Maintaining sterile conditions during the inoculation process is of the utmost importance since failing to do so will cause the loss of the complete fermentation batch.
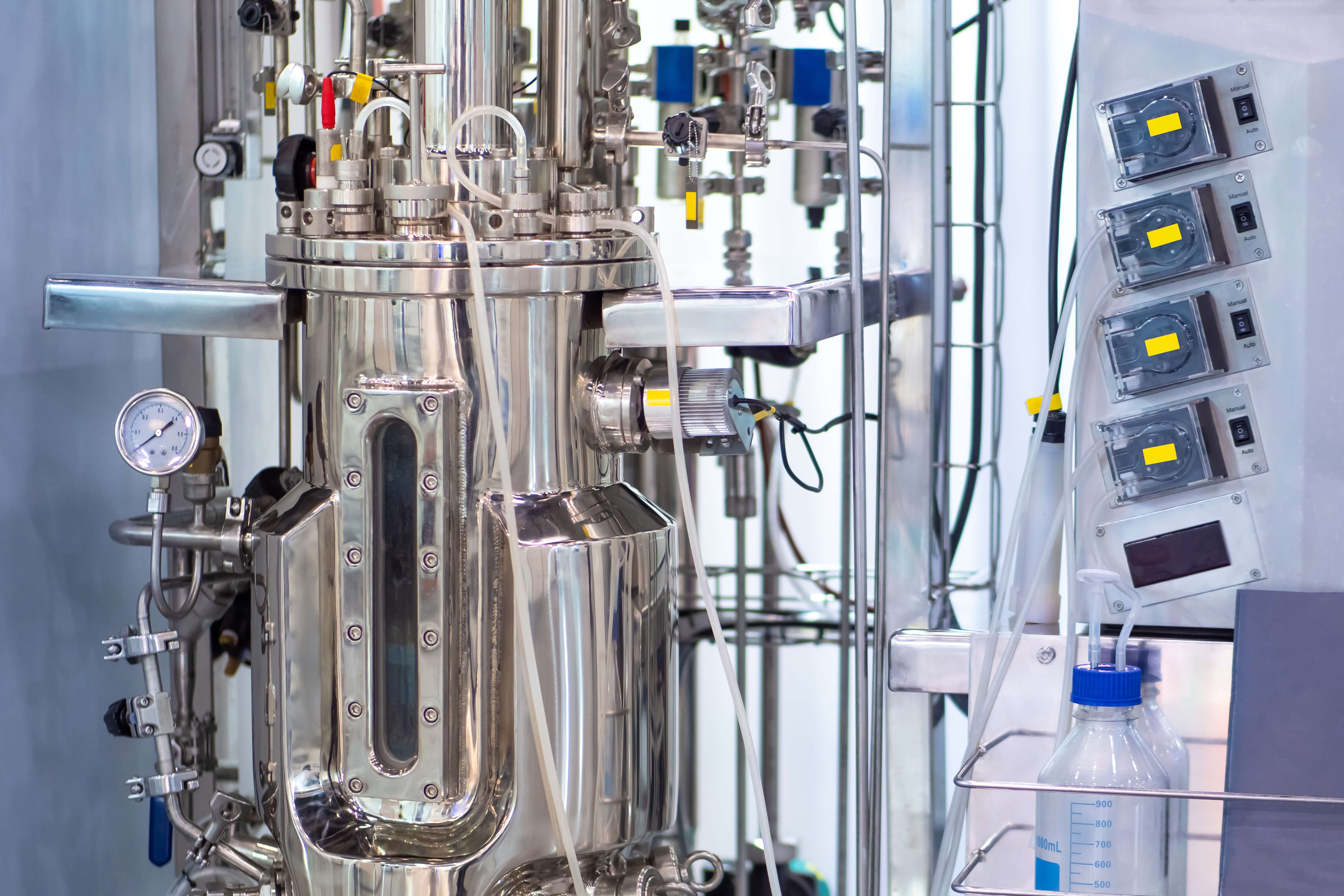
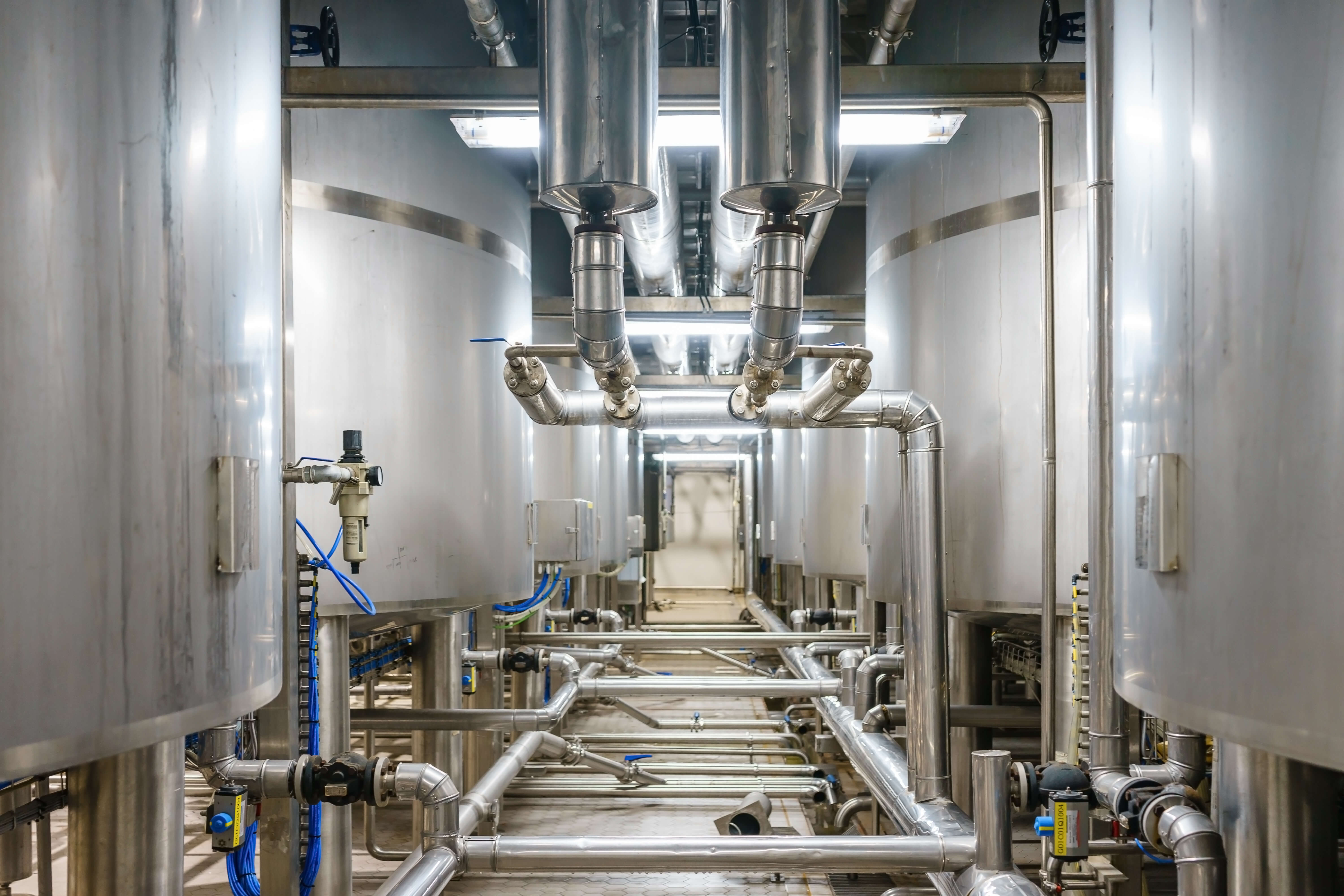
- Nutrient addition – There are many bioreactions where additional nutrients are added to the initial fermentation media during the fermentation process. This enables longer-lasting reactions, but one must also ensure that the introduced nutrients are sterile. Therefore, the bioreactor must be designed with proper sterilization systems, using sterile filters or heat, to ensure the nutrients do not introduce any foreign cells.
- Sterilization – Before starting the bioreaction, the bioreactor must be thoroughly sterilized. This is most often done by injecting steam into the bioreactor and maintaining a high temperature for a period of time.
- Sampling – Even when doing something as trivial as sampling, attention is required since this can introduce foreign cells into the culture that might contaminate the whole batch. Thus, the bioreactor must be designed with proper sampling systems that allow operators to take samples without any risk of contaminating the culture.
- Exhaust treatment – Sparged gases that are not absorbed must be expelled from the bioreactor to prevent the pressure from building up. The exhaust system must be equipped with filters that allow the excess gas to leave, while maintaining the sterility.
- Temperature control – The microorganisms produce heat as they grow, and the excess heat is usually removed by circulating cooling water in a jacket around the bioreactor in order to maintain an optimal temperature.
All Alfa Laval fermenters comply with the most stringent hygiene standards to ensure a successful fermentation/bioreaction process.
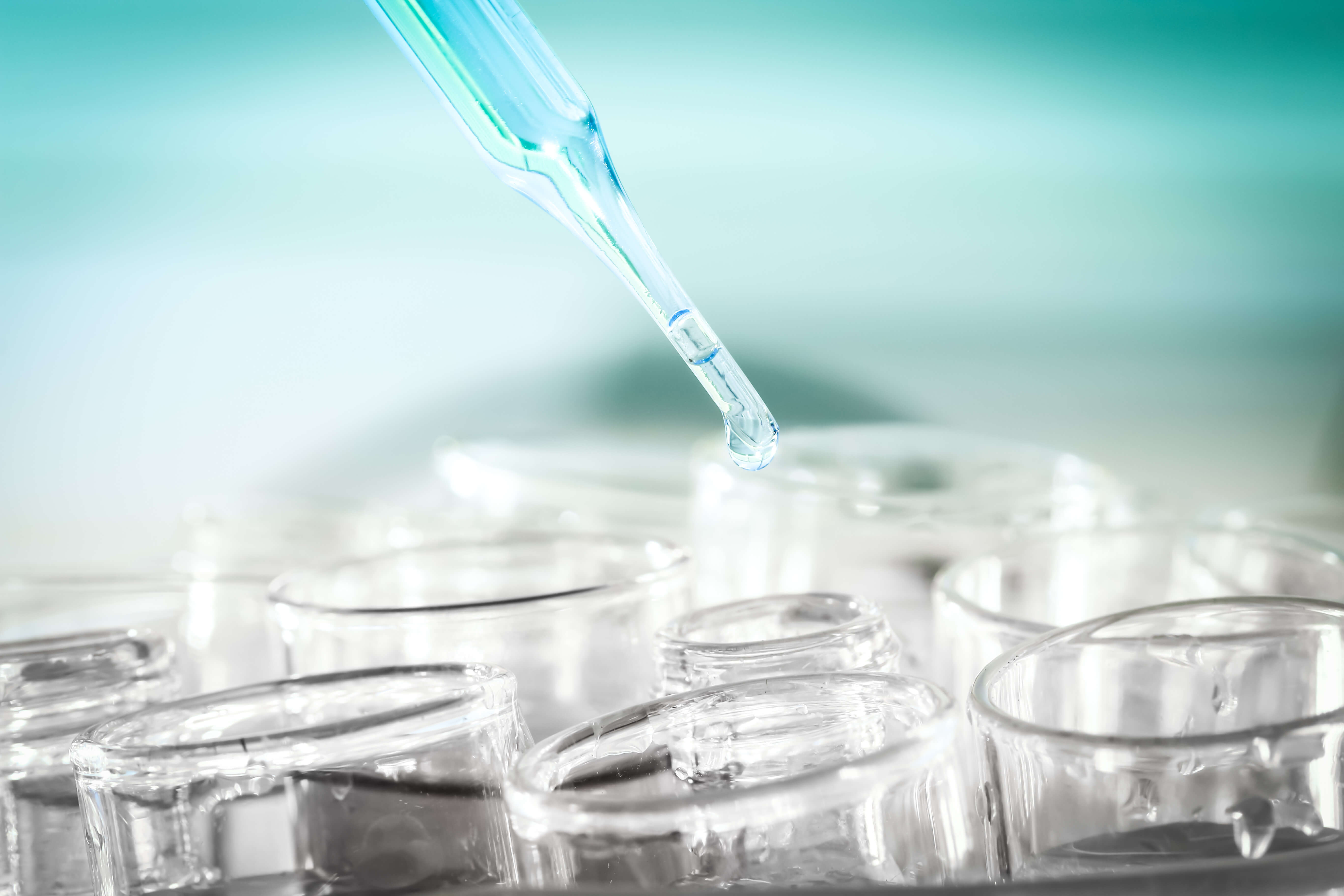